Cómo se rediseño el Koh-i-noor
Nueva versión del Koh-i-noor
Gracias a la tecnología de inyección de plásticos se desarrolló un nuevo modelo del tradicional secarropas para el mercado brasileño.
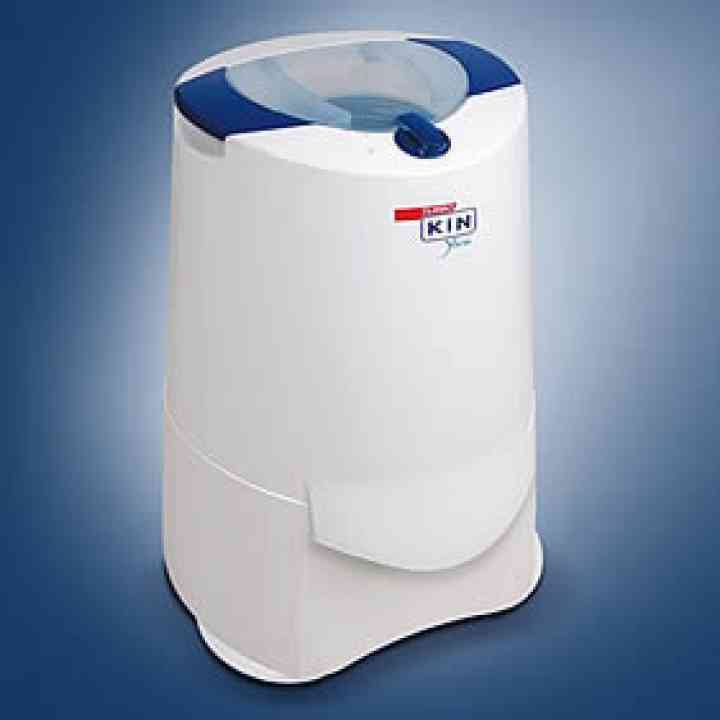
- Opiniones:
- 8
- Votos:
- 14
Autosal S.A. es el fabricante de un producto emblemático y líder de ventas en la Argentina: el secarropas Koh-i-noor, marca que alcanzó entre el público la dimensión de denominador genérico de la categoría.
Cuenta con dos plantas fabriles en el país y una empresa subsidiaria radicada en Brasil (Curitiba) para quien se desarrolló el secarropas centrífugo Turbo KIN Yara.
Los secarropas centrífugos se utilizan particularmente en áreas urbanas —donde no se dispone de la posibilidad de tender ropa al aire libre— o en climas húmedos.
Ofrecen una solución para el secado en frío, casi a punto de plancha, de prendas lavadas a mano o en lavadoras de tecnología básica, y en lavadoras automáticas. Mientras que las primeras no centrifugan, los equipos de lavado automático lo hacen a una velocidad promedio de 700 rpm. Los secarropas centrífugos, en cambio, alcanzan velocidades de 2800 a 3100 rpm.
En Brasil, su uso no se encuentra tan extendido y el cliente atendía la demanda con productos importados desde la Argentina.
Los motivos del pedido de diseño
La decisión de comenzar a producir en su nueva planta de Curitiba y de ampliar su oferta con un producto innovador dio motivo a la contratación de Legaria D&E. El nuevo modelo debía mantener la tradicional calidad funcional de la marca e introducir un nuevo lenguaje estético que contribuyera al logro de metas comerciales más ambiciosas. El pedido fue recibido en forma oral. El objetivo era lograr un producto con una fuerte carga de innovación, para lo cual el cliente, consciente de las restricciones que la propia naturaleza cilíndrica del producto imponía en tal sentido, admitió la posibilidad de incrementar levemente el volumen para así tener acceso a nuevas posibilidades morfológicas. El cliente nos suministró información básica sobre los productos de la competencia que, junto a otros requerimientos de tipo comercial y productivo que fuimos recibiendo en las reuniones iniciales, permitieron la elaboración de la propuesta de trabajo.
La solución propuesta
En su evolución histórica, los productos de la categoría prácticamente no habían sufrido cambios en su morfología cilíndrica, íntimamente ligada al volumen del paquete electro-mecánico que contienen (impulsor + cesto de centrifugado).
Hay algunas razones para ello: durante décadas, los gabinetes se conformaron sobre la base de un cilindro de chapa de acero engrapada, modalidad que continúa vigente. Por otra parte, uno de los aspectos de mayor valoración es la compacidad, especialmente entre los usuarios que habitan en edificios de propiedad horizontal.
En este proyecto, orientado desde el briefing hacia la tecnología de inyección de plásticos, se cuestionó la concepción morfológica imperante y se propuso un punto de quiebre en la evolución estética de la categoría.
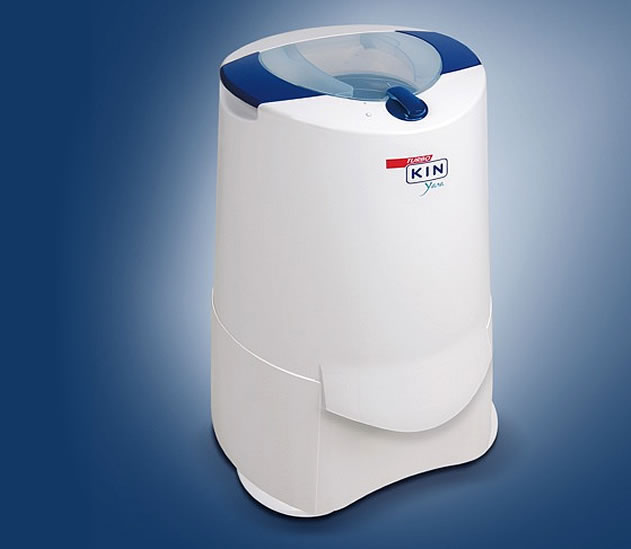
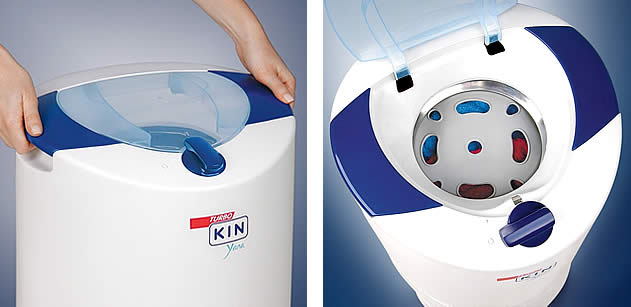
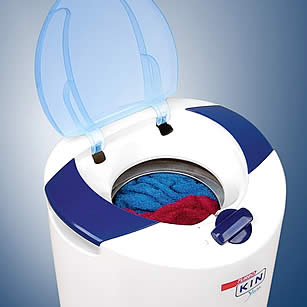
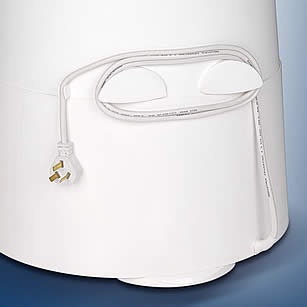
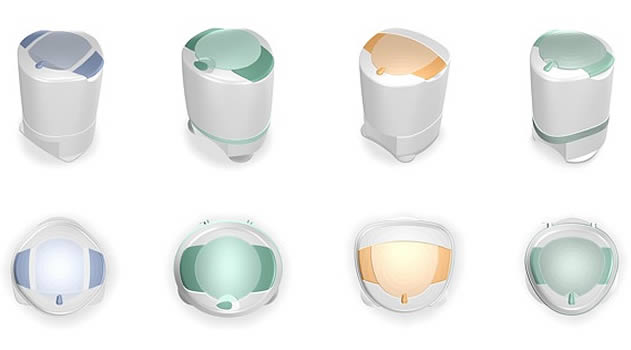
Sobre la base del conjunto electro mecánico y sistema de seguridad existente, el gabinete introduce un nuevo lenguaje formal que, de un modo sutil, abandona el paradigma de los contenedores cilíndricos. Este cambio se manifiesta en un cabezal integrado —puerta, perilla de comando y manijas de transporte— que implica una ruptura respecto de los gabinetes cilíndricos rematados por una tapa superior y permite apreciar el carácter «facetado» del volumen contenedor exterior.
Esta modificación conlleva dos apreciables mejoras a nivel perceptivo: por un lado, el volumen facetado, que se expresa claramente en la cara superior —una de cuyas «aristas» es tangente al frente del gabinete— transmite la idea de direccionalidad, (hay un frente y un detrás). Por otra parte, el volumen, levemente tronco-cónico, sugiere un apoyo al piso más estable.
Los cambios se expresan también en las nuevas soluciones morfológicas, de rasgos suaves, que definen a la boca de salida de agua —cuya depresión o contraforma inferior facilita el volcado—, a la base con cubre regatones y al enrolla cables ubicado sobre el lado posterior.
Extensión de línea
Una vez finalizado el Proyecto «Yara», tal su denominación comercial, la empresa Autosal decidió actualizar el diseño de sus líneas de secarropas producidas en la Argentina, y decidió incorporar los rasgos básicos de identidad del producto desarrollado para el mercado brasileño a los productos argentinos, a través de una intervención de menor magnitud que aquella, que resultara compatible con la tecnología de producción.
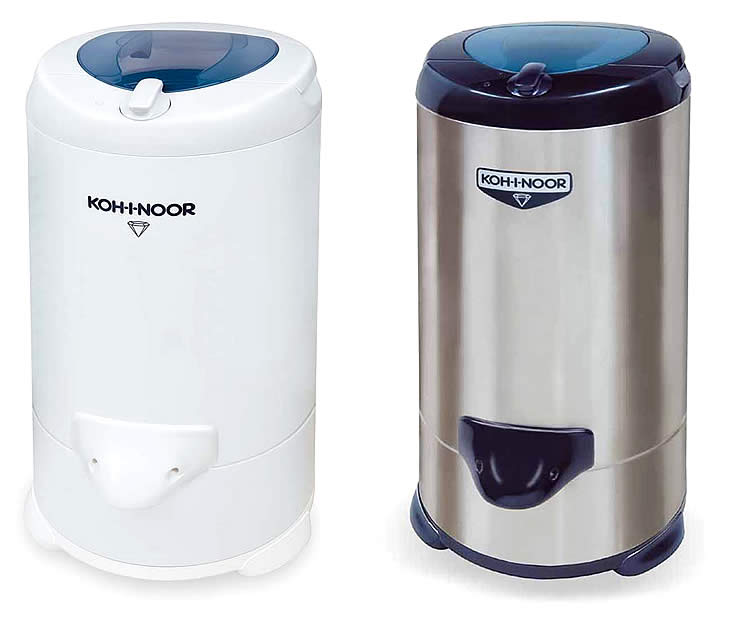
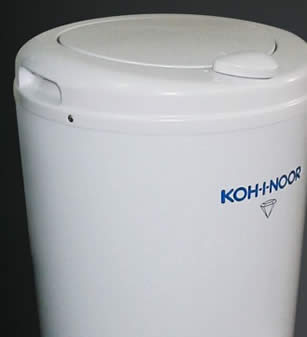
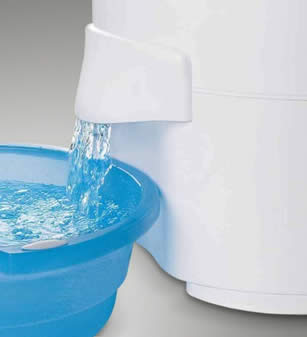
Fue una experiencia exigente e interesante. Ya no había posibilidad de modificar los volúmenes cilíndricos de los gabinetes, hecho que había constituido el eje rector del desarrollo original. El diseño se concentró, entonces, en el traslado de los recursos estéticos y soluciones mecánicas que contribuyeran a crear el «aire de familia» esperado. La actualización de diseño fue bien recibida por el público, permitió dotar de un estilo homogéneo a la oferta comercial de la compañía en ambos países y mejorar la aptitud de cara a su desempeño en el mercado global.
Preguntas
Se presentaron alternativas en la fase conceptual, todas ellas alineadas con el briefing acordado, pero con distintos grados de ruptura. Esto nos permitió medir el nivel de innovación con el que se identificaba el cliente.
¿Cuánto tiempo llevó el proyecto desde el pedido hasta la entrega de planos constructivos? ¿Realizaron prototipos durante el proceso de diseño?
Unos seis meses de trabajo de cierta intensidad. Luego, intervenciones ante requerimientos puntuales del proceso de ingeniería de detalle a lo largo de unos tres meses.
No se hicieron prototipos pues la prestación funcional no estaba en duda en este caso. En cambio, se elaboraron modelos de verificación estética en escala reducida, en la etapa conceptual, y en escala real en la etapa previa a la ingeniería de detalle, para eso se utilizaron tecnologías mixtas (artesanales y partes mecanizadas en madera en tecnología CNC).
Hubo mucha interacción y plena integración en la etapa de ingeniería, en la que colaboramos en la resolución de detalles para asegurarnos de que ciertos requerimientos propios de esa instancia no acabaran desnaturalizando el proyecto, más allá de concesiones atendibles desde lo técnico y lo productivo.
Información del proyecto:
- Cliente: Autosal S.A. para KIN (Curitiba, Brasil) (Argentina)
- Realización: 2005/2007
- Dirección: Hugo Legaria
- Equipo: Javier Molina, Héctor Turconi y Darío Polaco.
Temas abordados en este artículo
¿Qué te pareció?
Tu perspectiva es valiosa. Comparte tu opinión con la comunidad en el debate.
¡Opina ahora!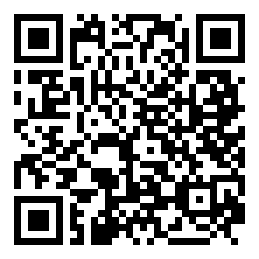
Este artículo no expresa la opinión de los editores y responsables de FOROALFA, quienes no asumen responsabilidad alguna por su autoría y naturaleza. Para reproducirlo, salvo que estuviera expresamente indicado, por favor solicitar autorización al autor. Dada la gratuidad de este sitio y la condición hiper-textual del medio, agradeceremos evitar la reproducción total en otros sitios Web.
Descargar PDFColabora con la difusión de este artículo traduciéndolo
Traducir al inglés Traducir al italiano Traducir al portugués